Fremveksten av CNC -maskinverktøy er en manifestasjon av en stor fremgang i bransjen. Det kan bedre løse problemene med rotete, fine, liten batch og skiftende delbehandling. Det er et følsomt og effektivt automatisk maskinverktøy. Når programmerere bruker CNC -maskinverktøy for behandling, må de først analysere prosessen. I henhold til informasjonen, generalisert form, maskineringsnøyaktighet osv. I arbeidsstykket som skal behandles, blir et passende maskinverktøy valgt, behandlingsplanen blir utarbeidet, behandlingssekvensen til delene bekreftes, verktøyene som brukes i hver prosess, Armaturen og skjærebeløpet, etc.
1. Rimelig valg av maskinverktøy
Når du maskinerer deler på et CNC -maskinverktøy, er det vanligvis to situasjoner.
Den første situasjonen: Det er et delmønster og et blankt, og et CNC -maskinverktøy som er egnet for behandling av delen, må velges.
Den andre situasjonen: Det er allerede et CNC -maskinverktøy, og det er nødvendig å velge deler som er egnet for behandling på maskinverktøyet.
Uansett situasjon er hovedfaktorene å vurdere informasjonen og typen av blanket, graden av forstyrrelse i den generaliserte formen på delen, størrelsen på skalaen, prosesseringsnøyaktigheten, antall deler og varmebehandling krav. Oppsummert er det tre poeng:
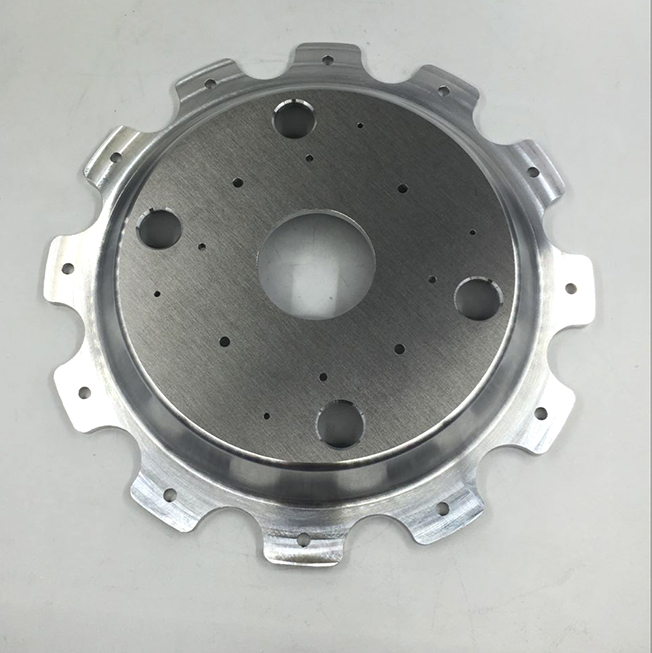
① Det er nødvendig å sikre ferdighetskravene for behandling av deler og behandle kvalifiserte produkter.
② Behandler til å forbedre produksjonshastigheten.
③ Reduser produksjonskostnadene (behandlingskostnader) så mye som mulig.
2. Analyse av teknologien til CNC -maskineringsdeler
Den tekniske analysen av CNC -maskinering involverer et bredt spekter av områder, så vi analyserer den bare fra de to aspektene ved muligheten og bekvemmeligheten av CNC -maskinering.
(1) Skaladataene på deletegningen skal samsvare med prinsippet om programmeringens bekvemmelighet
1. Dimensjonsindikasjonsmetoden på deletegningen skal brukes til egenskapene til CNC -maskinering. På delen av CNC -maskinering skal skalaen siteres med samme punktum, eller koordinatskalaen skal gis direkte. Denne markeringsmetoden letter ikke bare programmering, men letter også koordinasjonen mellom standarder, og gir stor bekvemmelighet ved å overholde konsistensen av design benchmarks, prosess -benchmarks, inspeksjons benchmarks og innstillinger for programmering. Fordi deldesignere generelt vurderer montering og andre bruksegenskaper i skaleringsmerking, må de velge delvise merkingsmetoder, noe som vil gi mye ulempe for å behandle organisering og CNC -maskinering. Fordi CNC -maskineringsnøyaktighet og gjentatt posisjonsnøyaktighet er veldig høy, vil ikke bruksegenskapene bli skadet på grunn av store akkumuleringsfeil, så en del av den spredte merkingsmetoden kan endres til den samme referansesiteringsskalaen eller merkemetoden som direkte gir koordinatet skala. .
2. Betingelsene for de flere elementene som utgjør delinduksjonen, bør være tilstrekkelige
Basispunktet eller nodekoordinatene skal beregnes under manuell programmering. Under aktiv programmering bør alle genomiske elementer som utgjør en del defineres. Derfor, når man analyserer deletegningen, er det nødvendig å analysere om de gitte forholdene til de få elementene er tilstrekkelige. For eksempel er buen og den rette linjen, buen og buen tangent på tegningen, men i henhold til skalaen som er gitt på tegningen, når tangenstilstanden beregnes, blir det krysset eller separasjonen. På grunn av de utilstrekkelige forholdene til de konstituerende elementene, er det umulig å starte programmering. Når den møter denne situasjonen, bør den løses gjennom samråd med deldesigneren.
(2) Strukturen og håndverket av hver prosesseringsdel av delen skal samsvare med egenskapene til CNC -maskinering
1) Det er best å velge den samme geometri -typen og størrelsen for hulrommet og formen på delene. Dette kan redusere verktøyspesifikasjonene og antall verktøyendringer, lette programmering og forbedre produksjonseffektiviteten.
2) Filetstørrelsen på den indre spor bestemmer størrelsen på verktøydiameteren, så filetradiusen til den indre spor ikke skal være for liten. Delens prosessbarhet er relatert til høyden på den bearbeidede summeringen, størrelsen på overføringsbueradius og så videre.
3) Når delen freser bunnplanet, skal ikke rillefiletradiusen R være for stor.
4) Konsekvent referanseposisjonering skal brukes. I CNC-maskinering, hvis det ikke er noen konsistent referanseposisjonering, vil reinstallasjonen av arbeidsstykket føre til inkonsekvens i orienteringen og omfanget av de to ansiktene etter maskinering. Derfor, for å unngå forekomsten av de ovennevnte problemene og sikre nøyaktigheten av den relative orienteringen etter de to klemmeprosessene, bør en konsistent referanseposisjonering velges.
Det er best å ha passende hull på delene som posisjonsreferansehull. Hvis ikke, sett prosesshullene som posisjonsreferansehullene (for eksempel å legge prosesslugger på blank eller innstilling av prosesshull på margen som skal freses i den påfølgende prosessen). Hvis prosesshullet ikke kan lages, bør det ferdige utseendet i det minste brukes som et jevnlig mål for å redusere feilene forårsaket av de to klemmen. I tillegg bør den også analysere om den nødvendige maskineringsnøyaktigheten og dimensjonstoleransene til delene kan sikres, om det er overflødige dimensjoner som forårsaker motsetninger, eller lukkede dimensjoner som påvirker prosessorganisasjonen.